PREDICTIVE MAINTENANCE is one of the formats of PREVENTIVE MAINTENANCE. The objective of this format is to decide the right moment to act just when it is really necessary, neither before nor after. This way, we will achieve a lower maintenance expense minimizing the operating costs of the buildings.
But first of all, let us analyse the etymology of the words:
- Predictive comes from the Latin praedicere, which means ‘to say before’
- Maintenance comes also from the Latin manus tenere, which means ‘to hold his hand’, in the sense that one person holds the hand of another to help him, to preserve him from any evil that may happen to him…
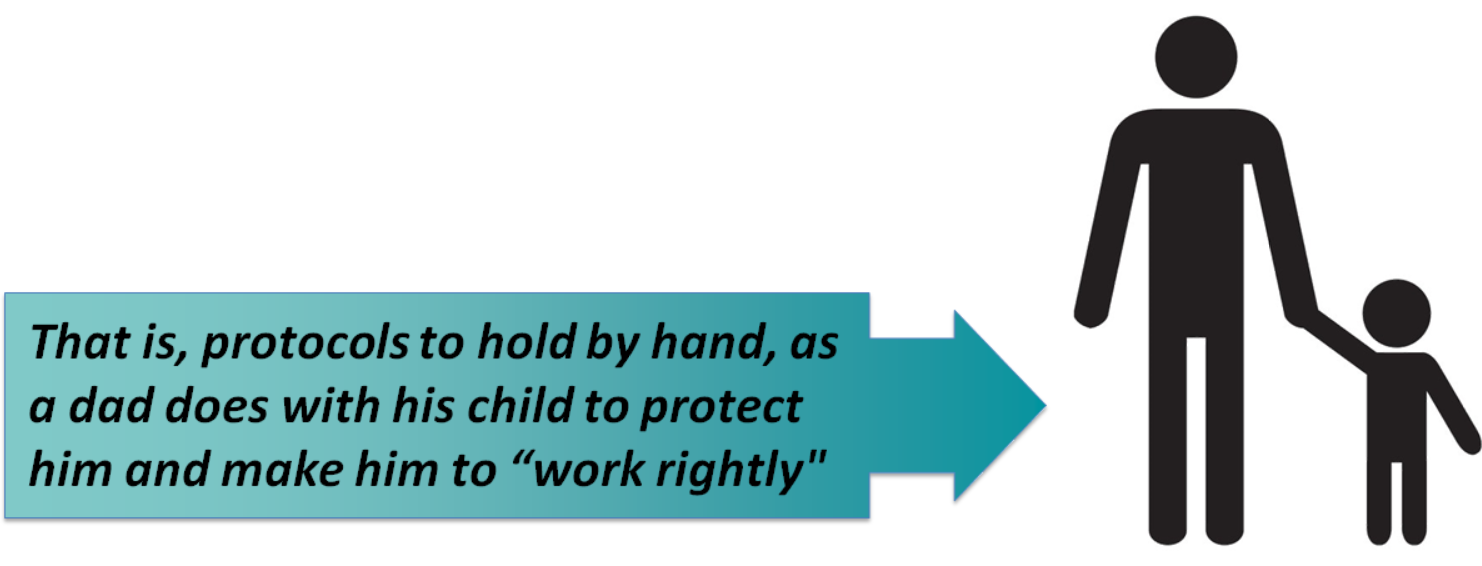
As simple as that. Within the three categories of maintenance…
- Conductive
- Preventive, in its various formats (chronological, frequency of use, regulatory)
- Corrective (or curative), with its versions of great corrective, substitutive, etc.
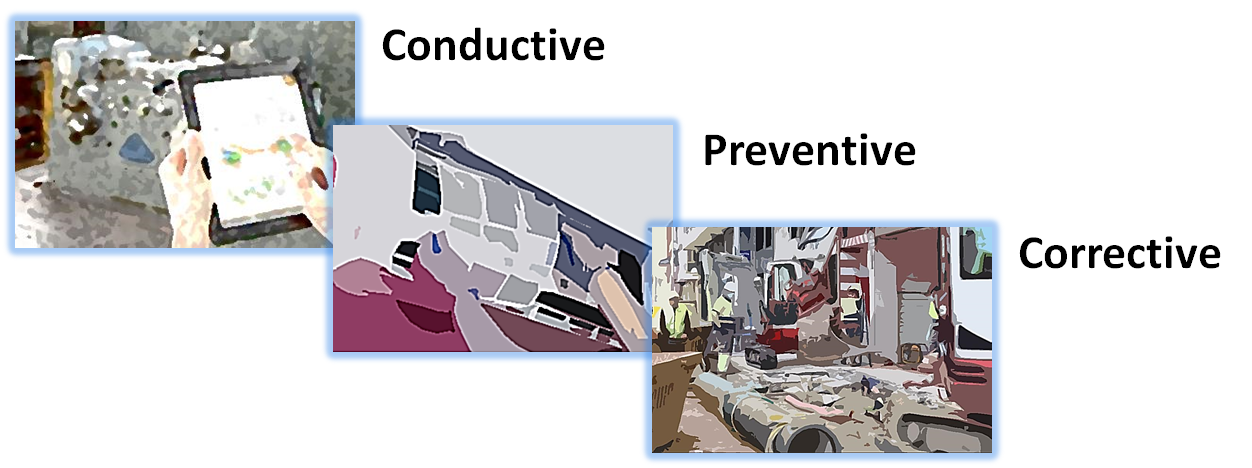
…Predictive Maintenance is just one more form of Preventive Maintenance.
Predictive Maintenance is the challenge of the future in the world of Maintenance. But not of a distant future. All the necessary ingredients to implement Predictive Maintenance are already there, at our disposal. We only need to realise this and start working.
The purpose of Preventive (attention, not yet Predictive) Maintenance is to act on assets before a breakdown occurs, before the asset becomes “out of service”.
But preventive action, which is also from the Latin praevenire, meaning ‘to come before’, has to be ordered by someone and for some reason…
…The “reason” can be from time to time. For example, every six months. Experience has shown that by cleaning the filters of an Air Handling Unit (AHU) every six months, its functionality is assured, and we can accept that users who benefit from the service provided by the AHU in that room will not see their comfort altered. But what would happen if we clean the filters every ten months instead of every six months? Maybe nothing would happen, because probably that room is only occupied during the mornings. But since we have obtained the value (six months) from many experiences, to be on the safe side, we reduce the time between interventions. And WE LOSE OUT.
Well, let’s now to improve the algorithm. We will launch the preventive maintenance order consisting in cleaning the filters, not every six months, but every 800 hours of operation. Therefore, we change the chronological frequency by the frequency of use, which seems much more reasonable.
But one must beware, because two identical AHUs providing comfort to two identical rooms that operate exactly the same number of hours, does not mean that the filters get equally dirty. One room has an occupation density of 8m2 per person, the other 16m2 per person. In one room the user personnel are from the project office, in the other the personnel come from the building site, and they transfer dust from the building sites they visit every day. Then, the number of hours does not help us either. And as we need to cover ourselves, the experience will bring us to reduce the number of hours to establish the frequency to prevent the breakdown from occurring. And WE LOSE OUT AGAIN.
Because really, when exactly should we honestly clean the filters? Well, it is very simple. When during the peak air conditioning demand, the indoor comfort conditions (temperature and diffusion speed) can no longer be reached, and subject to other possible factors being previously discarded. And we know that this happens when the pressure loss caused by the filter reaches a certain value.
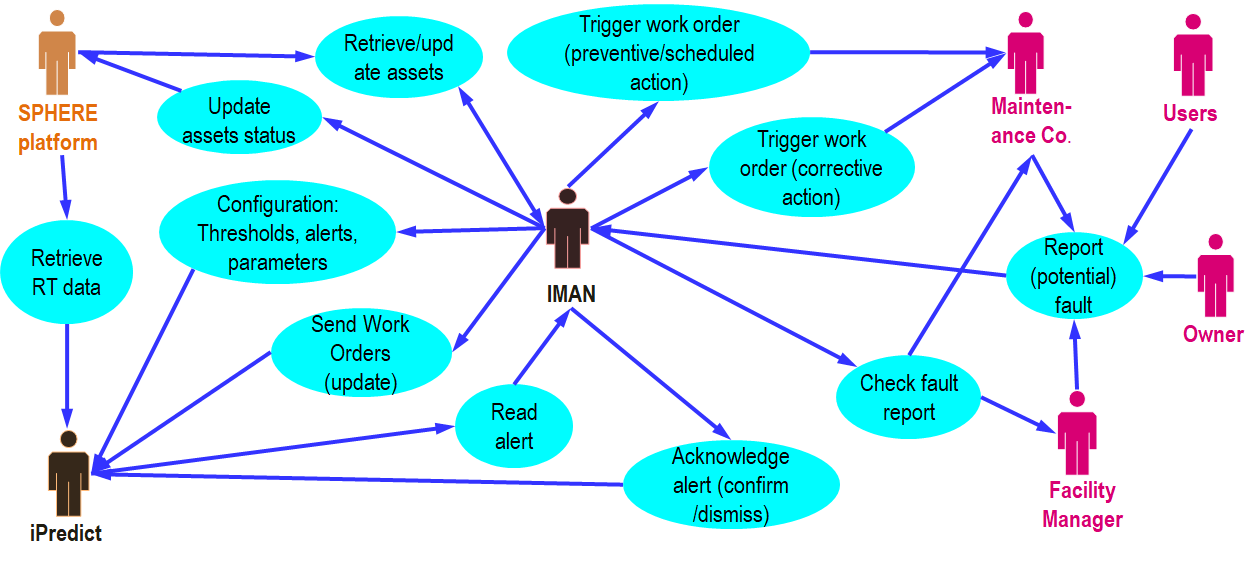
Well, that’s it! we have got the solution. Just before the comfort conditions (temperature and speed of diffusion) are no longer met, someone talks to us. We are calling for a prediction. And that’s where we will find a close relationship between the loss of pressure in the filter and the loss of comfort in the room. You are welcome: THIS IS CERTAINLY A PREDICTION!!
In doing so, we will be able to apply the preventive measure just when it is necessary, not before, when it is not yet required. Therefore, we do not lose out. We do not lose money. In consequence, at no time will users stop receiving the service, nor the level of comfort agreed.
But as we have explained in this example, we need “someone to tell us something“, and most importantly, to tell us before the failure occurs, before the committed service values are lost.
But, who is the “someone“? The someone is a SENSOR, a meter, a transducer: of temperature, pressure, flow, level, humidity, air speed, illuminance, strain, energy consumption, etc.
And who is the “something“? Well, the something is simply an ALARM, a warning, containing more or less additional information.
And how do we move from the SENSOR to the ALARM?
Also, very easily. The SENSOR, the transducer, measures a parameter and informs us of its value with the frequency required in each case. It can be every minute or every three months. Each case will have its appropriate time slot. With this information monitored and the technical knowledge of which the value is for which there is a risk of the failure occurring, of not reaching the set values, an algorithm is elaborated, so that when certain conditions are met, it will send an ALARM to the Computerized Maintenance Management System (CMMS).
Then, a technician of the Maintenance or Facility Management teams, will judge and filter that ALARM, and once ratified, the CMMS will issue an order for Predictive Maintenance (predictive because “We were told”) through the CMMS, in this case the cleaning of the filters of the AHU, just when it is necessary. Neither before because it would be a waste of money, nor after because we would do not reach the Service Level Agreement (SLA) of an Energy Performance Contract (EPC), thinking in an Energy Services Company (ESCO).
To setup what we have just said, what do we need? SENSORS, communication systems, IoT technology, and software for: data debugging, self-learning algorithms, trend and variable behaviour analysis, alarm emission, Predictive Maintenance orders issuing.
And nowadays, all these items are available, absolutely everything, with a very wide and reliable selection, at very low prices.
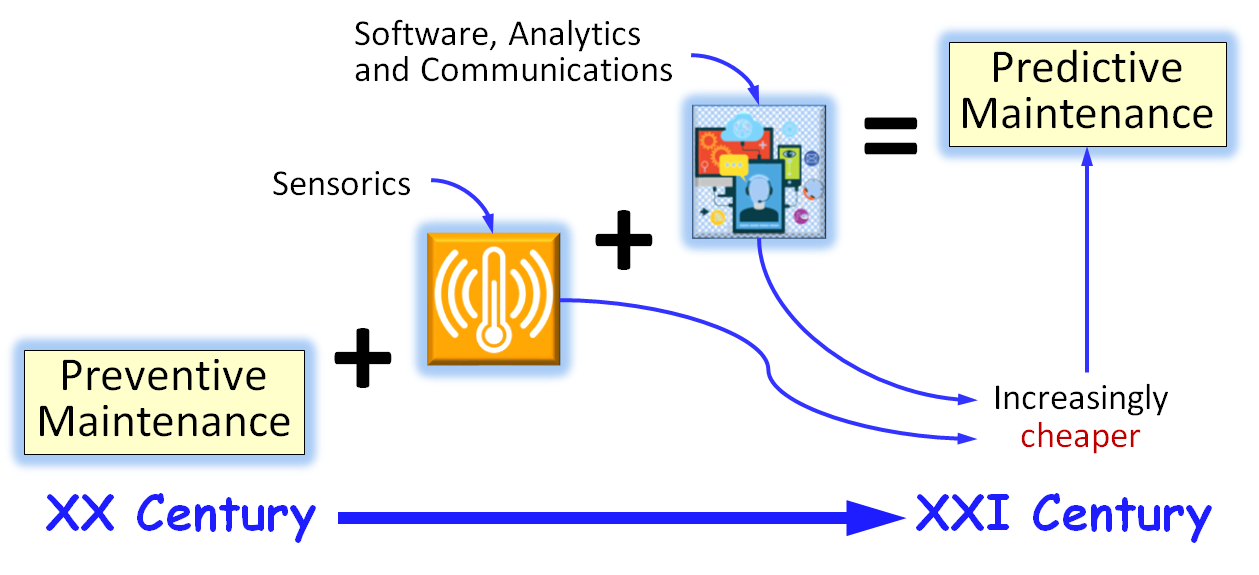
All right, so what is needed to eradicate Preventive Maintenance from the face of the earth and replace it with Predictive Maintenance? We only need to realize that we are in the year 2020, that the 20th century ended twenty years ago, and that Preventive Maintenance, as it has been done since the beginning of time, seen from the eyes of the 21st century, is a nonsense, is a relic of the past, and it has to be replaced by Predictive Maintenance based on information adapted to each case and to each situation. And this way we will not lose out. This way WE WILL WIN!!
We will earn money, ensure comfort, avoid the unavailability of services (lifts, lighting, HVAC) plus all the indirect economic savings that result from this, and we will raise the prestige of our buildings and infrastructures by switching to Predictive Maintenance.
So, let’s not waste any more time and get to work! What we have just described is, no more and no less, than the integration of Predictive information with the CMMS of buildings.
Written by Antoni Quintana and Enric Ortega, from COMSA.