The boom in the construction industry does not stop, and with the increasing consciousness about resource and waste reduction the sustainability impact of a building becomes more and more important. Building managers and investors can achieve energy efficiency targets by implementing sustainable materials and practices along the complete life cycle of the building as it is important to not only focus on green concrete. Following this concept, we will now dive deeper into the life cycle of sustainable buildings and concrete structures. For this, it is important to consider the complete life cycle, from design and construction to operation, maintenance and, ultimately, deconstruction. Let’s have a look at each stage and see how digital tools can help to reach this goal.
The Lifecycle of a Green Building
Sustainability does not only refer to the use and application of materials alone. In a wider sense, the lifecycle of a building has a major impact on how sustainable it really is over time. The lifecycle spans from the design and construction of the building to operation, maintenance, renovation, and deconstruction, so a sustainability focus in all stages can help reduce the overall environmental impact of the building. During the design stage, for example, using BIM and VR technologies enable planners and architects to ensure fast and reliable planning, while the construction stage calls for sustainable materials and processes. Maintenance and renovation of a building depend on the performance of the used materials, so a long-lasting construction can significantly reduce the amount of refurbishment. Durable construction products reduce maintenance needs, which, in the end, does not only lower the environmental impact, but also helps save costs.
Overall, there is a lot of potential to achieve sustainability targets in the construction industry, and innovations will further spur the adoption of efficient building materials and processes.
Designing Sustainable Structures From the Start
The biggest potential for making a building more sustainable lies in the design phase. Here, fundamental decisions can be made, for example by optimizing floor space area in relation to enclosed volume or by using higher strength concrete to optimize resources of a structure.
Planning a construction project involves both thorough attention to detail and a flexible response to changing requirements. Often, the two are not easy to balance, and this is where the Online Planning Tool can provide valuable assistance. Specifications can be easily created, including the download of a report, all relevant technical data, and Revit (IFC) objects to be used in virtual design tools that connect the digital planning process with real-life data.
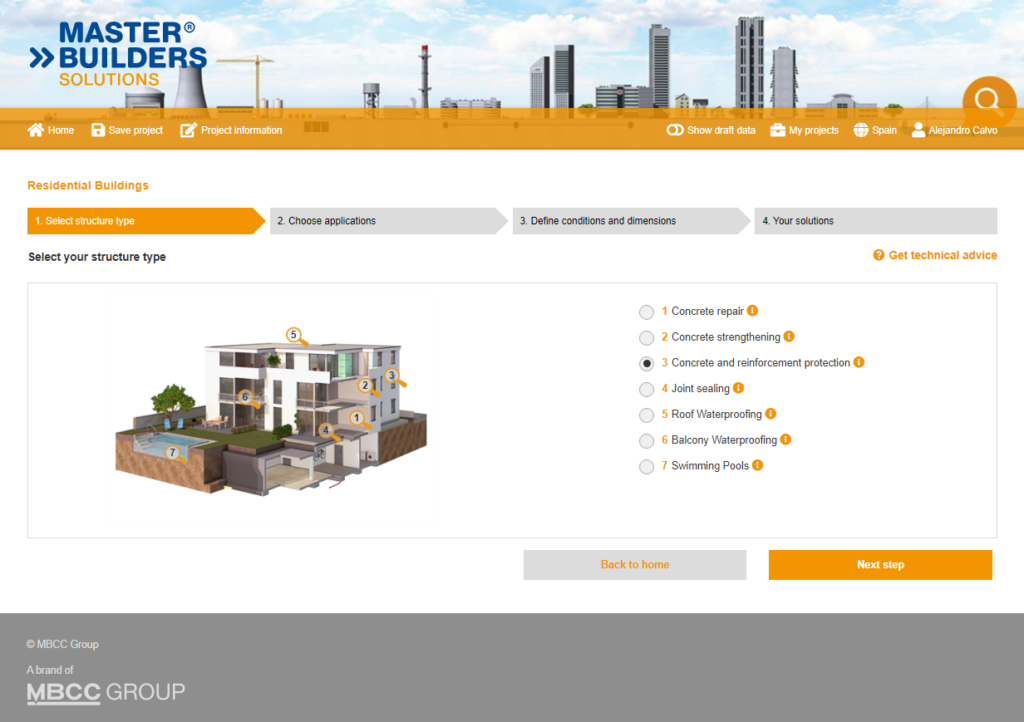
When you start designing a new building or structure, you can directly integrate sustainability for long-term performance: eco-friendly materials, low clinker cements and concrete admixtures, as well as alternative fuels and more efficient production procedures lower the carbon footprint. In addition, there are further measures which can extend the service life of concrete structures. Waterproofing, for example, can protect against deterioration of concrete as water is often an ingredient in concrete degradation processes.
Who Was OPT Designed for and What Kind of Information Does It Provide Customers With?
The OPT provides online specification support for planners, guiding them to a complete solution adjusted to the project requirements and complemented with all the required documentation: datasheets, certificates, specifications and BIM objects. At the moment, engineers benefit the most from the Online Planning Tool, since the first published scenarios represent more solutions for infrastructure and industrial applications, but thanks to Sphere Project we have included additional scenarios involving design aspects such as solutions for repair and maintenance, retrofitting structures, roof waterproofing, and entire area of decorative flooring solutions, with the aim of providing useful information also for architects and designers.
Figure 2. Anticarbonation coating Figure 3. Corrosion inhibitor
Figure 4. BIM content creation for construction materials
How Does the Tool Work and What Benefits Can Users Derive From It?
It is quite simple and straightforward. The Online Planning Tool has been devised and developed strictly from the user’s perspective, and it follows a clear logic. In the first place, the user has to select the general area in which he/she is looking for a solution, e.g. concrete repair areas, roof waterproofing. Then, in a matter of only a few clicks, the tool directs the user from specific applications and specific project conditions and dimensions to the appropriate solutions. All the important information and data including technical data sheets and BIM objects can be accessed and downloaded quickly, easily and from any device including a mobile phone or tablet, which means that the tool is also available for use directly on the construction site. All this helps users to define requirements and detail specifications, as well as BIM models to be implemented in the digital twin model of the building.
Why Is OPT an Interesting Tool for the Sphere Platform?
First and foremost, the Online Planning Tool is there to support those responsible for planning building projects and specifying construction materials. Working with the tool, users can access a lot of information and documentation by themselves and always get in contact with the corresponding department at MBS direct (technical department, specifications or sales) – and this, of course, benefits both parties. Customers obtain competent advice that supports or complements the information provided by the tool to ensure they are selecting a solution that perfectly matches their requirements. On the other hand, we receive customer enquiries with the project background and their specific questions and can respond to that in a much faster way – a real win-win scenario. The entire tool reflects the expertise of a group of architects and engineers involved in the development of the tool. The Online Planning Tool is available round the clock to help with general cases and, among other benefits, provides quick access to product information and documentation. All this is backed up by our experts to complement the services provided – a fact that makes the tool truly unique.
Constructing the Building
When the plans are in, the construction of the building or concrete structure can start. It is a fact that the construction industry accounts for a large amount of CO2 emissions. Therefore, manufacturers of concrete, chemicals and cement have implemented measures to make their products greener. For the construction of the building, however, it is not only the products themselves that increase the carbon footprint of the building. Reducing waste by less packaging, lowering the consumption of water and components as well as transportation of materials to the job site should be considered as they affect the overall sustainability of the building.
As long as all those factors are considered, the construction of the building will reduce the environmental impact.
Efficient Operation of the Building or Concrete Structure
The structure has been constructed and handed over to its designated purpose. Of course, the building manager or operator of the infrastructure will now monitor and optimize the energy consumption to reach energy efficiency targets.
The fact that proactive maintenance can lower the need for repairs, which would increase the carbon footprint, is not always known though and often receives insufficient attention: Keeping concrete dry using waterproofing membranes, for example, is an effective means of extending the service life of structures to withstand extreme conditions while ensuring constant operation.
Any damage in the structure can have dramatic environmental and economic consequences. On the one hand, there is economic loss if the damages force the operator to stop the activity and start unplanned maintenance or remedial operations. On the other hand, however, all repair and substitution works will necessarily create construction debris and will require the use of repair mortars and protection membranes, for example. All of this has an obvious environmental impact that can be significant if the structure requires major refurbishments.
Build a Sustainable Future
But what if there is a spalling in the concrete, a leakage in the roof or a damage on the floor? Repairs will correct this and thus put the structure back into operation. Refurbishment, however, can even further contribute to the sustainability of the building, while at the same time protecting investments – representing a smart way to extend the lifetime of the building.
Concrete, in general, is a durable product, and this longevity influences the service life of the structure. Consequently, extending this life cycle drives the sustainability of the concrete structure. Furthermore, repairing concrete before it cracks or renewing the waterproofing of roofs and walls can avoid downtimes, which are costly.
To sum up, the extension of the building life cycle will dilute the environmental impact. Therefore, it is important to integrate a focus on sustainability from the design phase on. However, even existing concrete structures can be made more sustainable: refurbishment and predictive maintenance are key to extending the service life and, thus, protecting investments.
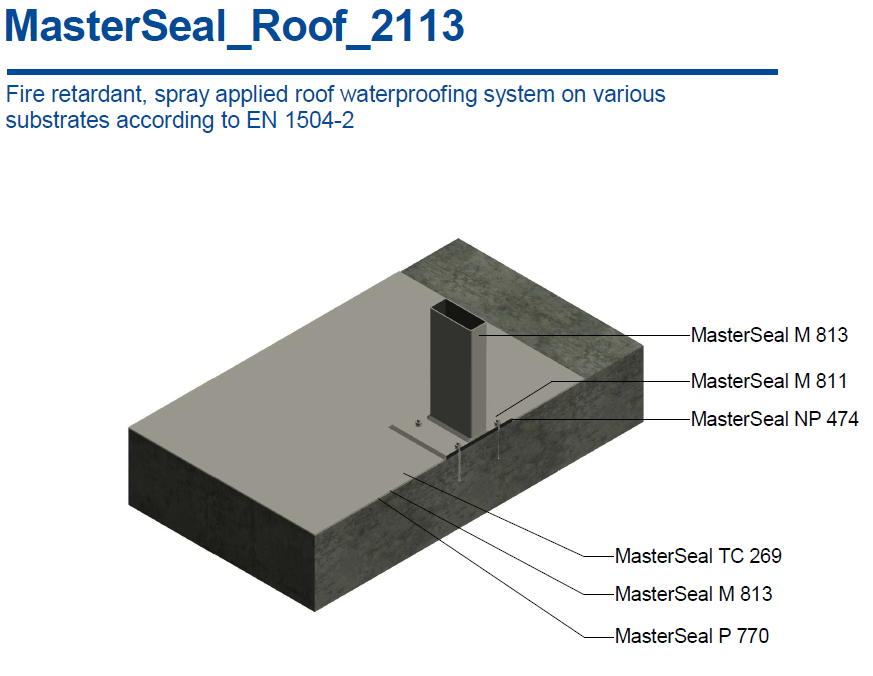
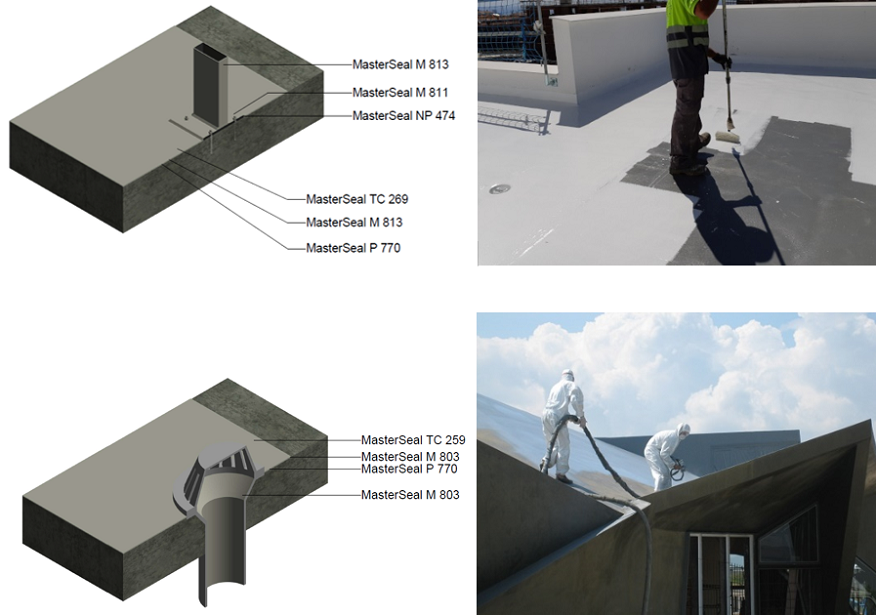
BIM Portfolio for Constructions Solutions
We also contribute in Sphere Project with the BIM content creation of construction solutions for repairing, strengthen and protect concrete structures.
This is the expertise that Master Builders Solutions can bring to the SPHERE Project: “We are very happy to support this EU project with our know-how and, with partners from ten different countries, work on the development and refinement of virtual building models”, says Olivier Bayard, Regional Business Segment Manager Admixture Systems Europe at Master Builders Solutions. “In this way, we want to contribute to an increased energy efficiency in buildings and to lowering the costs involved in construction projects. Designers and owners benefit from a digital-twin model across all project stages: from planning and design to construction and maintenance to demolition.”
Written by Alex Calvo, from Master Building Solutions